Last week I flew down to Japan’s southern island of Kyushu to visit the Toyota Kyushu Miyata plant and have a private conversation with the Toyota Production System (TPS) Promotion Office Director. Today’s post is about the Kyushu plant tour. My next post will be on my reflections from talking about Lean, education, and Toyota culture with the TPS Promotion Office Manager.
Tour of the Toyota Kyushu Miyata plant
The Kyushu Miyata plant tour was fantastic. The plant primarily makes Lexus vehicles and is known for its mixed model line.
The plant has won multiple J.D. Power awards over the years, including last year.
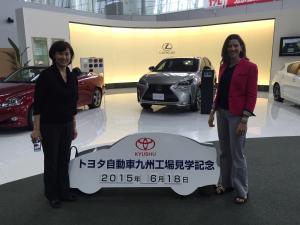
We spent 45 minutes viewing the large assembly portion of the plant. Like the plant in Toyota City that I visited in April, we got to view the plant from a walkway above the production line, which gave a great view of the action.Unfortunately, no photos were permitted, but I was able to take some photos of the display areas in the lobby.
This tour was entirely in Japanese, but my Japanese friend and colleague Miwa came with me and translated the tour and our visit with the TPS Promotion Office manager (though it was a good opportunity to practice listening to see what I could understand).
No. 1 Assembly Plant
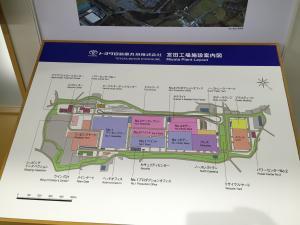
As we rode in the bus to the “No. 1 Assembly Plant”, we passed several buildings that house other parts of the process. The guide told us that the buildings at the plant were organized to follow the production process.
The guide also pointed out large chimneys that were painted yellow intentionally so that it was easier to see when they got dirty and needed to be cleaned.
Production control and andon support
Visual controls were used to display both current production control numbers and the location of andon requests.
Daily demand at the Miyata plant fluctuates based on customer demand, but on average the plant produces 13,930 cars per month.
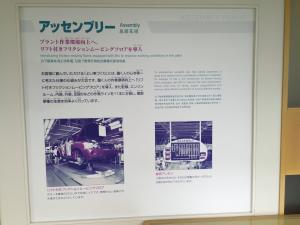
The production control part of the board showed that 443 cars were scheduled to be produced that day. 339 cars were schedule to be produced by that time of day, but only 326 cars had been produced. The board also showed the number 96% to show that reality was running at 96% of scheduled.
The andon portion of the board lights up red when any of the nine portions of the line are stopped. In the two minutes that I was watching, I saw about six new red andons come up onto the board.
I learned that the board only switches to red if the andon is pulled by the frontline worker and that the team lead can’t fix the problem before the line moves to the next station. There were likely many times that the andon was pulled by a worker, but that the team lead was able to resolve the issue before the line stopped and the light turned “red” on the andon board. It was easy to spot the team leads, as they wore slightly different hats and were always interacting with frontline workers.
If you want to learn more about andon, Mark Graban has written a good overview about andon at Toyota. I would agree with his observations that andon, and other principles that are core to Lean thinking and TPS, do not necessarily come naturally to the Japanese (or Westerners!). I’ll be writing about more of my observations about Lean thinking and Japanese culture in upcoming posts.
Lean production – just-in-time, jidoka and visual controls
It’s always impressive to see the Lean production principles in action at Toyota.
For example, there is a very low inventory of supplies that are highly coordinated with production, which are managed by a “just-in-time” process and kanban cards. We saw supplies arrive into the assembly area via a conveyor belt – already broken down out of boxes and ready to be installed. Our guide explained that there were two entry points for supplies – those that are manufactured onsite (such as many of the larger plastics) and those brought in from off-site (mainly the plant in Toyota City). Boxes are broken down outside of the assembly plant so that trash and additional dust are not introduced into the assembly area.
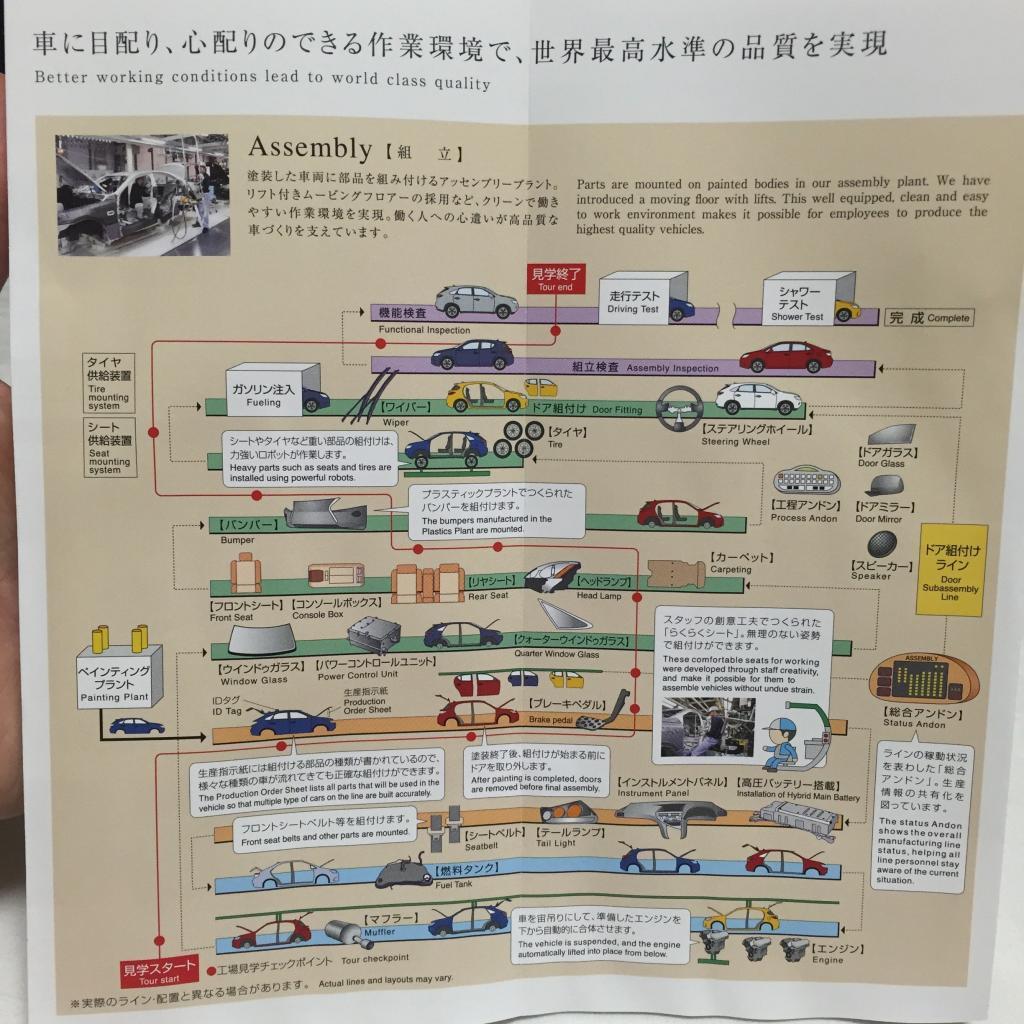
One of the striking aspects of the Kyushu assembly plant is the use of vertical space. After the engine is installed in the car, it is elevated to the ceiling for a portion of the process and then moved along the top of the plant to another line.
The daily production schedule also allows for a buffer of inventory between lines to balance the production so that not all lines are stopped when the andon is pulled. There were about four cars of inventory waiting up above to be moved along to the next step.
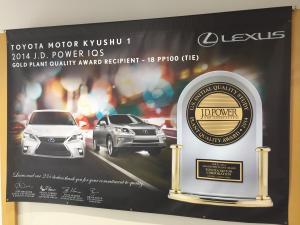
We also saw an innovation created by an employee idea that was called the “easy easy seat” (see photo above for a cartoon photo of the seat). The seat allowed the operator to move inside the front and back of the vehicle ergonomically, and included all necessary tools attached to the seat post.
An A3 size paper with all instructions is attached to the hood of each car. The paper has all of the specs and instructions for that particular car so that no worker has to rely only on memory.
The guide talked about the three concepts Toyota uses when applying jidoka (“intelligent automation”).
- Mistake proofing – to eliminate human error
- Dividing human and machine labor – for heavy things, machines should do it. For more fine or technical things, then humans should do it.
- Maximize human skill (a human can oversee multiple machines if parts of the process are highly automated).
Quality inspection
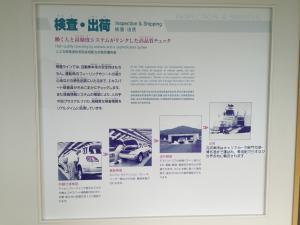
The total assembly time for each car is 19 hours, which includes five hours of quality inspection time.
Quality inspection involves both human and machine inspection and happens both inside the factory and outside on test drives.
We observed the first step of the inspection process called the “functional inspection”. A human drove the car forward, and machines tested the wheels, lights and other functions.
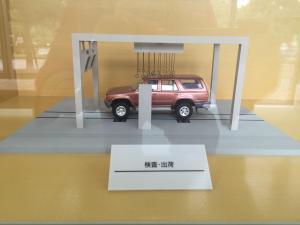
The photo on the left shows part of the inspection process – the worker pulls different levers, which in turn set off different tests.
The next steps in the quality inspection include a running test outside and a shipping inspection (including washing the car).
Is Lean or TPS easy in Japan?
The more I learn about Lean and TPS in Japan, the more I understand that it is not inherently easy to do just because people are Japanese.
In fact TPS seem to have been created by Toyota’s early leaders in many ways to be countermeasures to some strong Japanese traits such as maintaining harmony at all costs (such as not speaking up if there is a problem) and following rules just because it’s the way it’s always been done (but miss out on innovation and improvements).
There are also Japanese traits such as attention to detail and pride in one’s work that makes adherence to processes and routines much easier than it is in Western cultures.
I’ll continue to write more about my observations and reflections about Lean versus typical Japanese business culture in future posts.