On Monday I had the honor to spend the day with Isao Yoshino, a 40-year Toyota executive and one of John Shook’s first managers at Toyota, and visited one of Toyota’s Japanese assembly lines.
While it is always impressive to see the Toyota’s production principles in action, spending the day with Yoshino-san talking about leadership was one of the highlights of my time in Japan to-date.
CLICK HERE to get a curated PDF of 10 Toyota leadership lessons that Mr. Yoshino has shared with me.
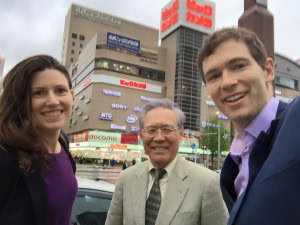
I had the pleasure of meeting Yoshino-san for the first time at the Lean Coaching Summit last summer when I had just learned that we would likely be moving to Japan. Yoshino-san accompanied us on our tour of the Motomachi plant in Toyota City to give his additional commentary, and then spent the afternoon talking with us about Lean, leadership, and Japanese culture over lunch and at his office. My husband took the day off of work to get to take advantage of this special opportunity to learn TPS from the source.
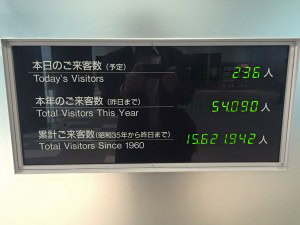
Yoshino’s reflections on Lean Leadership at Toyota
Here are some of the key take aways from our conversations with Yoshino-san.
Believe in kaizen
The most important thing for a manager or leader to believe in is the importance of kaizen. You don’t have to be an expert in the actual work process, but you must be serious about how to appreciate the concept of kaizen, of change and continuous improvement.
Create trust. Be consistent. Celebrate the attempt, not the outcome. Failure is the source of so much learning.
Be persistent
When Yoshino-san went to the U.S. to train the General Motors managers as part of the Toyota-GM joint venture NUMMI, he was told often, “Yoshino, it’s not easy to change culture”. But NUMMI showed that you can. Be persistent. Keep doing it. Keep saying it.
Go to gemba to show you care
One of the first things I was taught about the difference between Lean management and traditional management is that Lean managers “go to the gemba” (the place work is done). I’d always thought that the primary purpose was to go collect facts and understand what is actually happening. However, Yoshino-san explained that his main purpose to go to gemba is to show you care: “going to gemba makes people feel like they are important.” You then can see the facts as they actually are, but your primary purpose is to show you care about the people who do the work.
Teach the process of HOW to solve problems
Managers first must set the target (“this is the result I’m expecting”) and then show the person how to achieve the goal. However, this is not about giving the person the manager’s answer to the target, but rather show or explain the process by which the manger would go about achieving the goal.
Training can provide knowledge and change your mindset, but knowledge is not enough. Yoshino-san and others put the GM managers at the NUMMI plant through an initial three-week training course, which helped shift their mindset. But the real learning only came when the leaders and trainers showed them on the shop floor how to manage, and helped them practice and change their behaviors.
The words you use are important
“Share” rather than “teach”. Share your knowledge, experiences and way of thinking. Don’t set out to “teach” someone.
Be patient
Sometimes people are not ready to hear your experiences or knowledge. You have to show them. Start acting the way you want them to act. Show the results of your actions. You will create interest (or “pull” in Lean terminology). They will likely then ask.
Find the good
A good manager or coach finds the good in people – as a human and with their skills/thinking.
Build rapport and trust. Take extra time to find out about someone. Be interested in them as people. You have to care. Respect is two ways. “Make a small effort to give a little bit extra every day”. The human connection matters. Show that you care.
Ask questions to find out where someone’s skills or knowledge is at. Don’t criticize the answers. Find the good in their thinking and ask “why” to learn more. A “yes” mode is so important.
Toyota plant tour
As part of our day with Yoshino-san, we went on one of the standard tours offered daily. We were not allowed to take photos at the Motomachi plant, but there were some interesting things to see at the on-site museum. I want to visit some of the museums that we didn’t get to, as well as take our four-year old to the factory – he would love the robots!
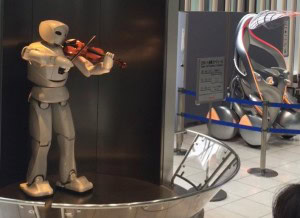
The first part of the tour took us through the welding area. As the tour brochure says: “high productivity and precision are achieve through the latest stamping machines and high speed transfer robots”. On the factory tour, we saw mixed models come through the welding line, where “robots weld about 400 body parts to form a car”.
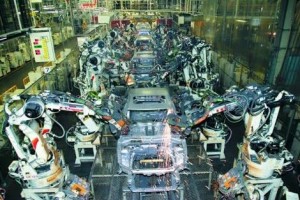
The second half of the tour was spent in the assembly area where we were able to look down at the production line from a catwalk above. Since there are no humans on the front line in the stamping and welding processes, and when we were there we didn’t see any managers on the line, it was hard to see much of the management system. It is when we got to the assembly portion of the plant that we could more easily see the management system in action.
Many people work in the assembly area – in conjunction with machines and robots to assist with the work. Team leaders wearing different colored hats were on the line, assisting front line operators whenever an andon light was lit up.
What do you think?
Of the leadership principles that Yoshino-san described, which ones resonate the most with you? What is your experience from going to the gemba and seeing Toyota or other Lean operations in action?
Share your comments below.
Sign up to receive updated blog posts
Last week I visited three other Japanese manufacturing organizations as part of a Lean study trip hosted by Makoto Investments. Sign up to receive notifications of new blog posts, including my reflections and photos from these tours.
[Update: posts about my gemba visits to Japanese organizations can be found on these links:
- An organization where the “only rule is ‘no rules'” – as a strategy to increase innovation and deliver value to customers.
- An organization that uses the basics of lean to “support every person to be successful”
- An organization that has created a deep practice of kaizen (continuous improvement) at all levels.