One of the presenters that I enjoyed the most at last month’s Australasian Lean Thinking and Practice Summit was Doug Rickarby from Toyota Australia. He shared his journey of working at Toyota from its beginnings in the 1980s to what will be its last run at the end of 2016.
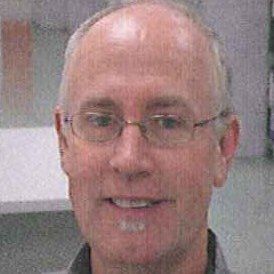
Doug is the Divisional Manager for Manufacturing Toyota Australia. He shared a personal and organizational story…that he described as both “human and Australian”.
What I found so powerful about Doug’s presentation was the human dimension of his story – the successes and challenges he and others have had in creating a Lean management system, and the true respect for people that is embodied by the Toyota Way.
[Note: This post is written from my notes from the conference. Thank you to Doug Rickarby for sharing such an important story at the conference and for supporting me sharing it with you. I’ve valued our dialogues recently about Lean leadership.]
Toyota Australia Overview
Some facts about Toyota Australia:
- Similarly to how Toyota entered the American market (with the NUMMI plant), Toyota Australia started as a joint venture with GM in 1989.
- 70% of Toyota Australia’s car builds are exported, primarily to the Middle East.
- It produces at a takt time of 121 seconds – roughly 435 cars a day come off the line.
- Employee demographics:
- 2500 employees
- 70+ nationalities
- average age = 44 years old (there are many long serving employees)
- 92% male
- The new model Camry that was released in May will be the last model produced in Australia. Manufacturing will cease at the end of 2017. Toyota Australia is actively seeking to facilitate job placement for its many employees.
Steps towards a Lean management system
Doug shared a story that sounds familiar to many of us who have been studying and applying Lean. When Toyota first took over the original Australian manufacturing, it was an organization that ran the line no matter if there were staff or supplies and that had a 70% turnover rate.
At first they focused on the tools of the Toyota Production System, but after several years they realized that the organization needed the management system to make everything work.
Internal competition
Toyota Australia was essentially competing with other Toyota plants for the decision for who could make the cars fastest and cheapest. In 2007 they realized that they needed to make an urgent change to keep up and be competitive with other Toyota plants worldwide.
A new strategy was introduced in 2007 with a focus on the outcomes and processes that they could control, such as safety, quality, cost, delivery time, attendance, etc. However, more improvements were needed to keep up with the rest of the Toyota plants.
Strategic management system improvements to stay competitive
In 2010, the Toyota Australia President introduced a 5 year plan that resulted in dramatic improvements for the organization, but they were not enough to save the plant.
Year 1 (2010):
- Hoshin (strategy deployment) with specific targets and clear metrics that were deployed by management level all the way to the shop floor (they called this the KPI tree)
- Matrix management – created “promotional” cross functional managers that were responsible for the deployment of a specific topics (such as Quality or Service)
Year 2 (2011):
- Employee development – focus on utilizing the appraisal system already in place, using A3s to give feedback to team leaders, and conducting annual team member assessments (such as ability to follow standard work).
Year 3 (2012):
- Supported supervisor problem solving – using information from the production control board.
Year 4 (2013):
- Team member engagement – focused on improving communication pathways. Sought out whether or not messages delivered were actual messages received.
- Managers asked three simple questions at the end of each communication to staff to reinforce the message and get feedback. (I am a proponent of leaders asking questions of inquiry and it was great to see Toyota Australia embodying this in their efforts to engage their people):
- What was the key message?
- What does it mean?
- Do you have any questions?
- Management also redoubled efforts to be in the gemba to support line-of-sight hoshin and to coach. Examples of time in gemba include:
- Monthly reviews (64 per month)
- Daily 3rd quarter “meeting blackout period” where no meetings are allow as to support management to be on shop floor (this is another example of how leaders can use a standard calendar to support managers getting to gemba).
- Monthly meeting by the President to review any work in progress.
Impressive improvements, but they were not enough
In year 1, Toyota Australia saw a 6.7% decrease in cost, and in Year 2 it saw a 7.07% decrease. However, 2012 there was a significant dip in sales to the Middle East, resulting in increased financial losses for the organization.
Despite the improvements made, they were not enough to overcome the challenges facing Toyota Australia. Ultimately, Toyota headquarters decided to shut down operations in Australia.
Doug shared how appreciative that he was that the President of Toyota, Akio Toyoda, flew to Australia to talk to the team directly and share with them management’s reasoning. This action by Mr. Toyoda speaks to the deep respect for people that is the foundation of the Toyota House.
Respectful transition
Mr. Toyoda’s words to the Australian team when he personally delivered his message that the plant would be shut down were: “I understand your passion and pride you have in your work, and I know this will continue until the last vehicle is built”.
Toyota Australia is embodying this spirit and is now focused on its transition to the future and its legacy. It’s top two goals are:
- Zero (0) Harm
- Respectful transition – “Last Car = Best Global Car”
Toyota Australia’s strategies to improve its business are having a positive impact on the business. This month, Toyota Australia posted a large profit after years of being in the red. Unfortunately, the results Toyota Australia worked so hard to achieve have come to fruition too late to save the plant.
People are the most important
Doug ended with what I think was the most valuable take away about Lean from the conference:
- Tools are important
- The management system is more important
- People are the most important.
What a powerful reminder to us all that at the end of the day, it is people who matter the most.
In the spirit of people mattering the most, many wonderful Toyota employees will be seeking other employment once the plant closes. If you are in Australia, consider these great people.
More learning at Toyota – site visit to Toyota Kyushu
I have the honor of visiting another Toyota plant in Japan next week – this time with a personal tour and visit with Toyota’s Kaizen Office Director. I also learned more about what separates Toyota culture from Japanese business culture (can you guess what that might be?)
What questions do you have and would like me to ask? Please write in the comments below or reach out to me via email.