Following our tour of the Toyota Kyushu plant, which I wrote about in an earlier post, my Japanese colleague was able to set up a personal meeting for us with the Toyota Production System (TPS) Promotion Office assistant general manager. We spent 90 minutes together talking about the role of the TPS Promotion Office at Toyota, TPS learning and development pathways at Toyota, and about TPS culture in general.
This conversation was conducted in Japanese, with my colleague interpreting, while I practiced listening and talking a little bit (chotto!) in Japanese. It’s not easy to get a personal meeting at Toyota and I appreciate my colleague’s facilitation to make it happen.
Lean and TPS isn’t easy – and Toyota isn’t perfect
One of my biggest take aways from the meeting is that implementing Lean or TPS is not easy, no matter if you work at Toyota, you are Japanese, or if you are in another company or from another country.
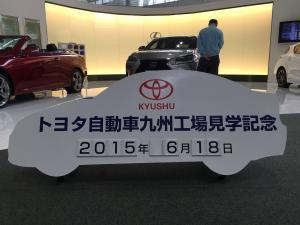
I really appreciated the manger’s candid remarks about running the TPS Promotion Office and their role as coaches in the organization. He shared similar challenges that I’ve experiences in the same role at a large healthcare organization in the U.S. and that I know many others have faced.
Toyota isn’t perfect and doesn’t have everything figured out, but it is continually improving as an organization and with it’s management system.
If you are interested in learning more about Toyota and other Japanese organizations implementing Lean, you may be interested in checking out some of my earlier posts from gemba visits in Japan. Check out the “gemba visit” category to the right.
Overview of the TPS Promotion Office
We spent the first part of our conversation talking about the purpose and management of the TPS Promotion Office.
Purpose
The TPS Promotion Office is responsible for conducting TPS education, training, and coaching for three primary groups:
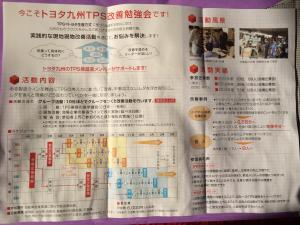
- Internal staff and managers
- Suppliers and other companies associated with the company
- External companies that are in other industries (non-auto)
The goal of all three is to help raise the competencies and thinking of Kyushu people and industry as a whole.
I found it interesting that there is a split at Toyota about what type of people development HR is responsible for and what the TPS promotion office does. While the TPS office trains leaders though the pathway described below, HR is officially responsible for training courses on general “leadership” and “communication” skills. I would have thought that these functions might be combined at Toyota.
Roles and development
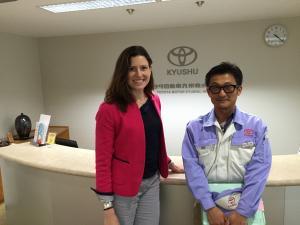
There are 35 staff in the TPS Promotion Office and all staff are on two-year rotations. A typical TPS promotion office staff member tends to be hand-picked as high potential future administrators, managers and leaders. They are usually more junior in their career – perhaps 3-5 years after joining the company – and after two years they move into a more senior role in the organization. This next role is not specified when they come into the department, but Toyota always finds a leadership position for the managers rotating out of the TPS Promotion Office.
The two-year rotation training includes 12 educational units, followed by going to gemba to practice and goach. The rotating staff members learn from more senior staff members, who in turn then teach the next generation of rotating members. Staff also go outside of the office to teach and learn in the gemba out on the shop floor.
Competencies
We asked how staff members’ competencies are assessed. The manger had recently taken on the leadership position for the Promotion Office and said that he was in the process of developing a more robust competency assessment that would be completed when someone joins the office and then every six months of their rotation.
TPS training and development pathway for employees
The manager shared a document that illustrates the TPS training and development pathway for internal Toyota employees – from new hires to plant manager.
There are three pathways that staff join Toyota – frontline operators, administrators, and engineers. All three pathways receive training and development, but there are some differences in the content.
The training consists of both didactic modules and some experiential learning, and they vary in length from a few hours to many days. My explanation below comes from both what the TPS Promotion Office manager shared, as well as my Japanese tutor’s translation of the details not shown in the photo below.
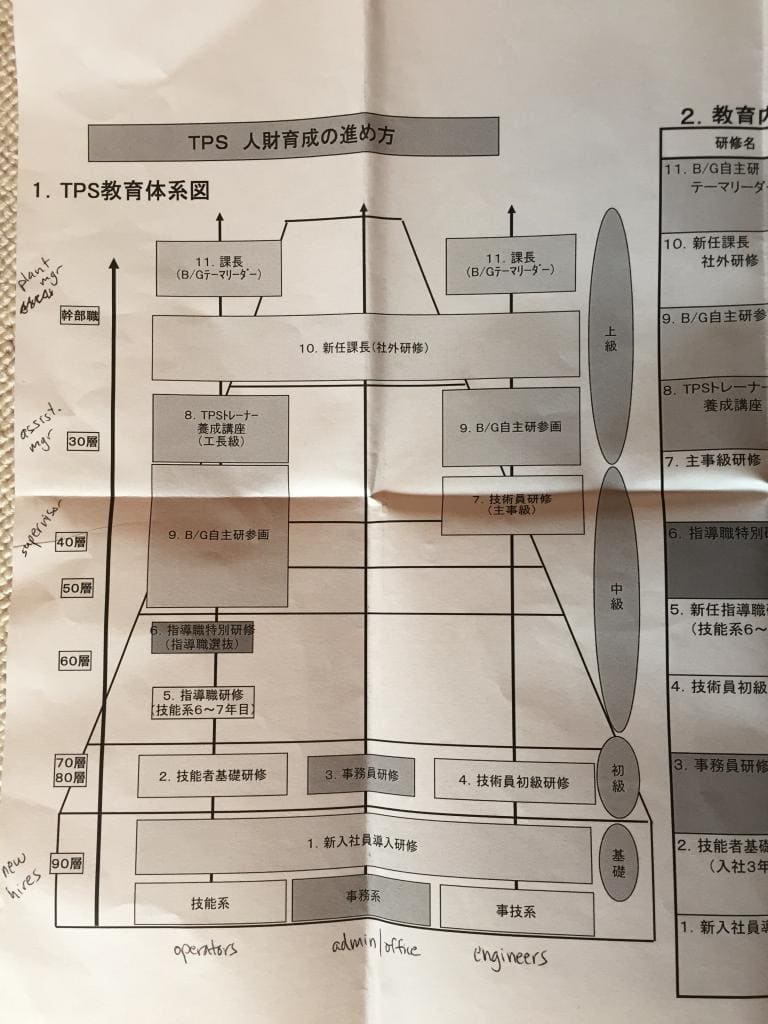
Step 1 consists of basic education that happens for all new hires that focuses on an introduction to TPS (including a “lego exercise”), TPS history, and a lesson in what to do if there is a problem (“stop it, call for help, and wait”). Steps 2, 3 and 4 are continued basic training that focuses on understanding an “efficient way of thinking” and about kaizen.
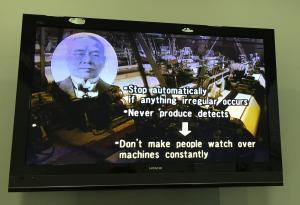
Operators have additional training focused on deeper understanding of kaizen (5) and how to understand, manage and improve standard work (6).
In step 7, participants must teach the basics and do a kaizen in their own gemba. In step 8, participants are taught how to be a professional and leader of a whole company.
Before moving into management roles, employees must go through step 9, which is called jishuken (management driven kaizen activity). The TPS Promotion Office manager shared that this is when people from different groups come together to solve a problem. The manager-trainee serves as the team lead for the group. This process is not done through the “kazien workshop” weeklong workshop that we are familiar with in the West, but rather it is a small group that comes together four times to work on a specific problem. The TPS Promotion Office manager believes this is a really good experience in learning how to work with other people. For himself, as an engineer, it was a way to learn to work with operators and people from other backgrounds so that he would be more successful once he became a manager.
At level (10), which is required for managers no matter what stream they entered the company, a manager has to go to a different industry to lead a team that is learning TPS. As managers get more senior in the organization, they need to be able to interact more with outside vendors and suppliers. This training opportunity gives them some of this experience.
Leadership skills in the gemba
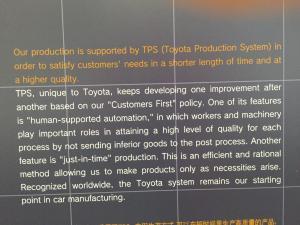
The manager shared that even at Toyota, personal management style makes a big difference in each leader’s capability.
For example, not all managers go to gemba as frequently as others. The TPS promotion office coaches sometimes must suggest that the managers to go to gemba to see what is going on.
Since the TPS Promotion Office members spend much time in the gemba, they often see what is happening more that some managers might. Instead of telling the manager what is going on, it is better to say “you should come to gemba and see with your own eyes”. Leaders need to develop the habits to support improvement in their areas.
Sign up to learn more from the Toyota visit
Before I visited the Toyota Kyushu plant, I posted on social media to see if anyone had questions for me. I asked a few of the questions that were posed, and they provided some of the most interesting insights of the day. I’ll be sharing these insights in my next post. Sign up below to be notified when it is published.
What is your experience?
If you have been an internal or external consultant for Lean, process improvement or leadership development, what is your experience? What challenges have you found in teaching people how to think critically or lead differently? Please share your thoughts and questions below.