As part of my week of healthcare related conferences in Japan several weeks ago, I traveled to Fukuoka to attend the 3rd Conference for Healthcare (CHC).
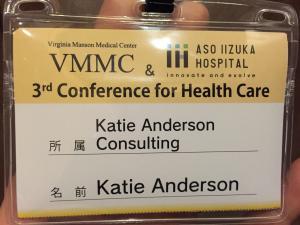
The conference is jointly hosted by Aso Iizuka Hospital, which I visited in July, and Virginia Mason Medical Center, which was one of the first healthcare organizations in the U.S. to start practicing Lean.
I wanted to attend the CHC to learn more about how hospitals in Japan are thinking about quality management, process improvement, and Lean, and I wasn’t disappointed.
I was also looking forward to meeting Dr. Gary Kaplan, CEO of Virgina Mason Medial Center and Chairman of the Board for the Institute for Healthcare Improvement, and Diane Miller, Vice President at Virginia Mason, who both gave several talks over the course of the two days.
Japanese hospitals are not Lean, but they are learning
Given that many manufacturing companies in Japan have been practicing Lean for decades – and that the Toyota Production System, the system that inspired the word “Lean”, is based in Japan – you might be surprised to learn that hospitals and many other non-manufacturing organziations do not use Lean. I certainly was when I moved here in January!
I’ve written about my observations about Japanese healthcare management in previous blog posts as well as the Lean Post over the past year.
While Lean is a relatively new concept for Japanese healthcare organizations, it is great that there is a conference to share what people are learning domestically and to bring in international speakers to advance the thinking about Lean and improvement.
A few examples of Lean experimentation
I was excited to hear that a few other organizations besides AIH (whose Lean activites I wrote about earlier this year) have been experimenting with Lean tools and concepts as part of their quality improvement efforts.
I made connections with both of these organizations and hope to be able to visit them (and some others) in 2016.
Rural public hospital
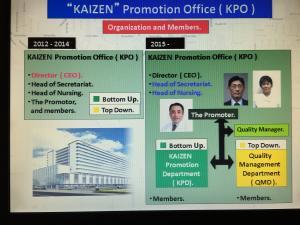
Ehime Prefectural Central Hospital, a public hospital on Shikoku Island, started a Kaizen Promotion Office in 2012.
They are using “top down” kaizen to focus on major quality issues and “bottom up” kaizen at the front line (such as 5S and kaizen rounds).
They are also using Quality Circles as a was to engage staff in improvement work.
Tokyo private hospital
St. Luke’s International Hospital in Tokyo has a strong quality management program in place. For the past five years, they have been bringing PDCA (Plan-Do-Check-Adjust) cycles and kaizen concepts to the front line.
However, like many hospitals around the world, “it is hard to do PDCA cycles with physicians”…
St. Luke’s desired outcome for kaizen is to “create an enabling environment where creating a kaizen culture is the responsibility of senior leaders”.
[Update: following the conference I have had several meetings and visits to St. Luke’s and have written multiple posts about what I’ve learned about their approach to kaizen, quality, leadership and more.]
Value Stream Mapping is a new concept for hospitals in Japan
Both Virginia Mason and the Directors of the Kaizen Promotion Office at ASH introduced the concept of Value Stream Mapping at the conference and how they have used this tool to drive improvement work.
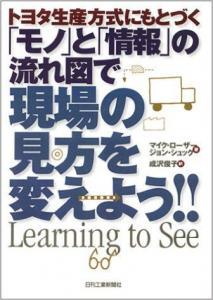
The session chair asked the audience how many people had used VSMs – I was only able to count six or seven people with raised hands (the two VM speakers, me, and a few people from AIH). A few more hands were raised when asked if they had heard of VSMs, but it was a completely new concept to most.
Learn to See
Value Stream Mapping was one of the first Lean techniques I learned. I found Mike Rother and John Shook’s book “Learning to See” a helpful explanation of the process. I found out recently from Mike Rother that the book is translated into Japanese.
I hope many conference attendees were inspired to look into how they can use Value Stream Mapping to support their improvement efforts and to better understand how their processes deliver value to their customers.
Make time for improvement
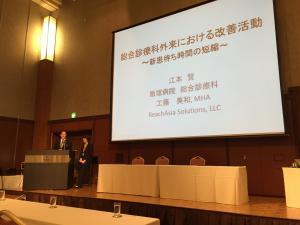
During Q&A, a nurse from AIH said that “we don’t have time to do improvement work” (such as going out to do actual observations), so that VSMs have been conducted from memory, rather that stepping out of the work to observe.
This reminds me of how challenging it is to start improvement work, but how important it is to have the time to improve. It is powerful to just stand and observe – when you are doing the work, you often miss what is actually happening.
If organizations want improvement, they will need to figure out how to support their staff to have time to do the improvement.
Lean is a management system, not just tools
Dr. Kaplan and Ms. Miller both emphasized that Lean is a management system, not just tools and techniques. Their experiences at VMMC are in line with my experiences supporting many healthcare Lean transformations.
I thought was a valuable opportunity for the Japanese audience to learn more about how the concepts that originated in their country as the Toyota Production System can be applied to improve their hospitals!
Some highlights from Virginia Mason:
- “We want to build the capability to learn and continue to adapt, rather than have high certainty that we have the right answers.” – Gary Kaplan
- Use “waste reduction” not “cost reduction” because focusing on cost often incentivizes the wrong behavior.
- “We call it [the Virginia Mason Production System] a management system – it is how we manage the entire enterprise.” – Gary Kaplan
- Include patients in your improvement work. They are your customers. A response to staff or physicians who are reluctant to include patients in improvement activity because of worries that they will see the “dirty laundry”: “don’t be embarrassed – they already know”. – Diane Miller
Chairman Aso’s Inspirational Case for Change
At the end of the first day of the conference, Chairman Aso, the head of the Aso Corporation that owns and manages Aso Iizuka Hospital, gave an inspirational keynote speech.
Chairman Aso met Gary Kaplan many years ago and started a partnership between the organizations. Both organizations send staff, physicians and leaders to the other organization on learning exchanges. This conference is also the result of that partnership.
Highlights from Chairman Aso’s keynote
Use Japan’s strengths to improve hospitals
“The Japanese people have many cultural strengths that support continuous improvement – teamwork, kaizen mindset, spirt, and loyalty. But why don’t we use these strength to improve hospitals?” – Chairman Aso
I found this comment by Chairman Aso an inspirational one. Much of what I have heard recently, including earlier in the week at an Innovation Summit, has been focused on what Japan is lacking.
While there are opportunities for improvement and areas in which some of Japan’s national cultural traits can be inhibiters to innovation and improvement, I liked that Chairman Aso framed his call to action in terms of Japan’s cultural strengths.
Build on these strengths and apply them to this industry! If Toyota can do what it has in the automotive world, why can’t the Japanese do the same to transform healthcare?!
Learn from other organizations, industries and countries
Meeting with Virginia Mason was an accelerator for Aso Iizuka Hospital to bolster its Total Quality Management program with Kaizen. Virginia Mason learned Lean by coming to Japan. Japan know can learn from U.S. hospitals like Virginia Mason.
Compete to improve
“The Japanese are competitive by nature” – He hopes that the conference will give inspiration and tools to get other hospitals started.
Japanese public hospitals also need kaizen
Chairman Aso wants to help transfer kaizen and TQM concepts to all hospitals – especially public hospitals. (In Japan, 30% of hospitals are private and 70% are public. Public hospitals in Japan are usually run by academic physicians who do not have management experiences, which is often mentioned to me as a barrier to improvement in hospitals).
He believes that public hospitals in Japan need more leadership. He said that “Abenomics (Prime Minister Abe’s economics reforms) wants hospitals to improve”, but to do that we need to change the leadership of hospitals.
He emphasized that kaizen is needed in public hospitals as well as private hospitals. Kaizen (Lean) could have a huge impact in Japan, but it is contingent on the driving force of leaders to lead change.
Every organization has its own learning journey
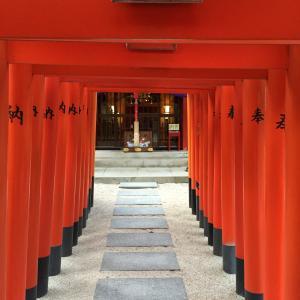
It was exciting to hear the excitement of the audience to learn more about Lean as a management systems and tools such as Value Stream Mapping. It reminded me of when I first heard Dr. Kaplan speak at the Institute for Healthcare Improvement in 2007 when I was just learning about Lean.
At that time, at Stanford Children’s we were starting with 5S and bringing some tools and techniques, such as kaizen events, to organization to do improvement work. But we did not really understand Lean to be a management system – yet.
We had to experiment and learn from our failures (and successes) to realize that we need the management system, as well as the tools, to create a sustainable system.
Every organization has to start somewhere to learn. And this conference was an opportunity to spark thinking and inspire improvement work from tools to a management system.
There is a huge opportunity in Japan to use its strengths, as Chairman Aso said, to improve healthcare!
It’s a great time to be here in Japan and I look forward to contributing to the ongoing learning in Japan and internationally.