I just got back from a week and a half trip to Japan to prepare for an upcoming Japan lean study trip I’m leading on behalf of the Ohio State University.
Any reason to visit Japan is a great one in my book, and I’m thrilled to be able to share my connections and insights with others on this upcoming study trip.
Update: we may have a few spots available to non-OSU affiliated individuals. If you would like to join us in Japan May 12-19, 2018, reach out to me!
5 Intense and Fun Days of Lean Learning
Our trip preparation was packed full of interesting learning experiences that I intend to write about in future blog posts, including:
- Spending three days with my friend and Toyota mentor Mr. Isao Yoshino, from whom I always learn words of wisdom and insights. (If you don’t have it already, you can get my top ten leadership insights from Mr. Yoshino by clicking here).
-
Dinner in Nagoya with Rick Guba (director of the OSU MBOE program), Mr. Yoshino, Mr. Sumiya of TMH, and our coordinator Mami. Visiting over 10 Japanese companies and organizations to learn about their approach to kaizen and respect for people including:
- Toyota itself in Toyota City
- two of Toyota’s Tier 2 and Tier 3 suppliers near Toyota City
- Ogura Metal, a gear company and a winery in the “5S Town” of Ashikaga
- Toyota Memorial Hospital
- a post office
- an elementary school
- and more!
- Learning about the “7 Minute Miracle” by talking with the former President of the Shinkansen cleaning company that is famous for its customer service and 7-minute changeover (which I mentioned in a previous post).
- Eating at the “lean” sushi restaurant chain I visited last May and visiting a “lean” public restroom that paralleled the one I visited years ago.
Plus of course, the always enjoyable rides on the Shinkansen and copious delicious Japanese meals.
I also added an extra visit with my friend Tim Wolput and visited in an accounting company’s engaging morning meeting (“chorei”) with him and Christoph Roser (check out the morning meeting I experienced with Tim last year too!).
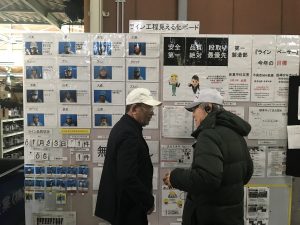
The uniting theme: Focus on people!
While visiting these organization and talking with their leaders, we learned a lot about respect for people, kaizen, and management, and saw some amazing production principles and visual management in action – and definitely opportunities for improvement.
No matter where they are on their improvement journey, what unites all of these organizations is their deep respect for focus on people first and foremost.
A reminder that Lean isn’t inherently Japanese
These experiences also confirm my belief, which I’ve written about many times on this blog, Planet Lean, and the Lean Post, that Japanese culture does not equal Toyota Culture, and that not all aspects of what we in the West consider “Lean” thinking and practices are inherently easy for the Japanese.
There is a tremendous amount of learning about lean thinking and practice that can be had in Japan. But it is clear that not all Japanese companies – be they manufacturing or other industries – are Toyota! How could they be?
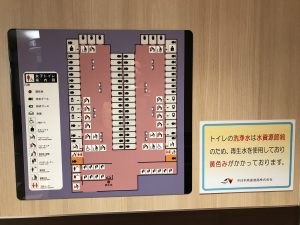
“Lean” isn’t a Japanese term
For the most part, as a term describing what we in the West know as management practices that originated as the Toyota Production System, “lean” (or a Japanese translation) does not broadly exist.
“Kaizen” is a common term, but “kaizen” does not encompass the wider management system that we often think of in the West when we think of “Lean management”. Similarly, many companies have a deep practice of TQM or other quality management practices – especially in healthcare – but this does not equate to what we in the West might expect to see from a “lean management system”.
As I wrote in a blog post after living in Japan for 14 months:
While in Japan, I’ve come to learn that what we in Western societies consider “Lean” is not inherently Japanese. Not all Lean practices are intrinsic to traditional Japanese ways of thinking and not all Japanese businesses are run like Toyota (or other Japanese organizations that we might label as “Lean” practitioners).
Response to the Wall Street Journal’s article about “Japanese Manufacturing”
A recent Wall Street Journal article titled “Companies Everywhere Copied Japanese Manufacturing. Now the Model Is Cracking” was published last week and has sparked a lot of commentary in the Lean community.
Several Lean thinkers that I know and respect wrote some great responses within 24 hours of the article that echo many of my thoughts on the subject and on which I commented, including:
- The WSJ Overgeneralizes about The “Japanese Model,” Not All Companies Are Toyota by Mark Graban
- Is there a crack in the model of continuous improvement? by Tom Ehrenfeld
- Countries Don’t Have Production Systems, Companies Do by Michel Baudin
My comments – its about reflection and learning
My comments on all three of these articles written in response to the WSJ article include a variation on the following thoughts (this excerpt from my comments on Mark’s blog):
One of the biggest takeaways for me from living in Japan for 18 months, and subsequent visits, is that not all Japanese companies have a kaizen mindset, and certainly the Toyota culture is unique.
I remember talking to Mr. Isao Yoshino, John Shook’s first manager at Toyota, two years ago about some recent scandals at Toyota and issues faced by other Japanese manufacturers. He told me that one of the biggest differences with Toyota is that it has a practice of “hansei” or deep reflection. The test for Toyota would be how it *learned* from its mistakes. He was not so sure the other companies had as deep of a practice of humility and reflection.
Yoshino’s reflection on these various issues across different Japanese companies was:
“If you believe you are perfect, you won’t find the answer. If you don’t believe you are perfect, then you are open to finding the answer. Once you are ready to accept that mistakes can happen, then you are okay because you will learn.”
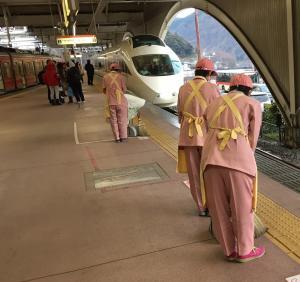
Apologies versus reflection and learning
The practice of formal apologies is deeply engrained in Japanese culture, as you can learn about here.
Friends and colleagues in Japan have told me stories of having to go through elaborate apology rituals for varying levels of business mistakes or social errors of propriety that occurred.
In all of the examples cited by the WSJ of these egregious errors by Japanese companies, you could search online and find pictures of the executives going through the formal apology kata (or ritual) of bowing and offering deep apologies.
Toyota’s deep practice of reflection
Since that initial conversation about the Toyota scandals and issues, Mr. Yoshino and I have discussed the qualities that he believes what sets Toyota apart from most Japanese companies – the humility and deep reflection and learning that is ingrained in the culture.
During those conversations, Mr. Yoshino expressed confidence that through hansei (reflection) practices that Toyota would uncover the root causes of their outcomes and course correct to ensure that they are not moving too far away their core belief in kaizen and the Toyota Way.
It’s not kaizen or PDCA without the “Check-Adjust”
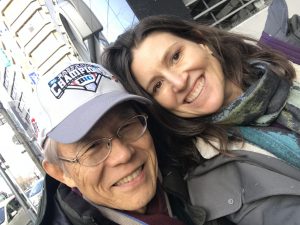
The improvement model of Plan-Do-Check-Act that Deming introduced to the Japanese is not complete without deep reflection that is required in the “check” phase, which leads to learning and adjustment.
For companies that attempt to emulate Toyota, the artifacts and production principles are easier to see and copy, but the deeper and essential practices respect for people and learning are the principles that are less visible and much more challenging to develop.
A question for these other “Japanese manufacturing companies” to understand their depth of “lean” thinking and practice is how much actual reflection and learning have happened as a result of these issues? How are they learning? How are they improving?
At the end of the day, its the people and the learning that is the most important!
More reflections and insights to come
In future posts, I’ll share more insights from this recent trip to Japan and other reflections on leadership, coaching and Lean practices.
Also if you haven’t already seen it, you can click here to get a PDF of the top 10 Toyota leadership lessons that Mr. Yoshino shared with me in 2015 & 2016.
Thank you for reading and, as always, I welcome your thoughts and comments below.
Gemba Academy podcast highlights
Also, if you missed it, I’m honored to have been included in Gemba Academy’s 200th podcast episode as a highlighted guest!.
GA 200 | What We’ve Learned from 200 Episodes with Ron Pereira and Past Guests