Last spring I led a study trip to the Japanese town of Ashikaga, which considers itself to be the “5S Mecca of the world”, to learn about how organizations in the town practice Lean management and how the concepts of “joy” and “revitalization” are a special elements to “Ashikaga-style 5S”.
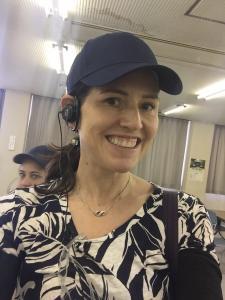
If you haven’t yet read the first parts of this series, I encourage you to visit them first to get context about the town of Ashikaga and a background on Ogura Metal.
- Japan Gemba Visit: Ashikaga Part 1 – the city that uses 5S to revitalize and bring joy to the community
- Japan Gemba Visit: Ashikaga Part 2 – Ogura Metal, using 5S and Lean to “bring smiles to all employees & customers”
This post focuses on how Ogrua Metal has put in place the principles of Lean, kaizen, and 5S and what I observed while touring the factory and head office.
Unfortunately, we we not permitted to take photos while inside Ogura Metal, but I have included photos from handouts that we were given.
Kaizen activities and the “Ogura 5S Way”
Mrs. Ogura, as I shared in the previous post, is an inspirational woman who has turned her family company from one run in a typical command-and-control style to one where employees feel engaged and happy.
Her enthusiasm for developing people and creating a positive working environment was palpable. During our visit, she explained how she brings the Ogura Production System (OPS) to life “to bring smiles to all employees and customers”.
Large cross-functional improvement
As we walked around the factory, Mrs. Ogrua explained that larger improvement activities include cross-functional teams working on longer-term kaizen projects.
Celebrate small improvements
Ogura employees also submit over 3000 kaizen suggestion per year for small improvements that can improve everyday processes.
This focus on and pride in small suggestions made by everyone has been highlighted in nearly every Lean practicing Japanese company I visited in the past two years, including others such as a rural family-owned electronics manufacturer and a large multi-national company.
5S is still hard
Interestingly, Mrs. Ogura made a comment that only part of 5S is inherently Japanese – the first “3S’s” of cleaning and organizing, but the final two S are challenging even for Japanese people. This echoes my conclusions from an earlier post that in Japan “clean is beautiful, but 5S is still hard”.
Factory tour – “5S Theme Park”
Our tour of the Ogura factory was not only inspirational because of the many many visual examples of OPS management activities (A3s, visual management systems, huge production boards, etc), but also because of the whimsical and fun way that Ogura employees have implemented 5S principles in the “Ogura 5S Way”.
The “Ogura 5S Way” really is an embodiment of spirit of joy and one couldn’t help but to leave our tour with a smile.
Each section of the factory has a different theme, chosen by the employees, to help bring joy to what might be a mundane work environment.
“Fruit stand” – Door Striker Quality Inspection
All workstations in the quality inspection area are decorated like fruit stalls.
Employees came up with this as a way to make their workspaces more enjoyable.
Mrs. Ogura said that “managers were not involved in this at all” – employees came up with the ideas and implemented it on their own.
The quality inspection workers in this area inspect over 30,000 door strikers per day (5 door strikers are made per car), which is 7000 parts per worker per day. The decorations make the environment more enjoyable and contributes to the productivity of staff.
“Grocery Store” – Shipping Inventory
The workers in the shipping inventory area in the warehouse chose a “grocery story” theme. Large cutouts of different types of food are hung above different sections of the warehouse. For example
- Flat things = “pizza”
- Iron plates = “steak”
- FIFO = “Japanese noodle”
Mrs. Ogura explained that, like food, the product area needs to be fresh and clean. They saw inventory decrease after implementing the food theme because staff were more engaged and also felt more responsibility of faster processing (as she explained “you don’t want food sitting around, so you don’t want inventory sitting around”, which led to employees were more aware and motivated).
“Magic Garden” – Standard Work display area
In this area of one of the main warehouse, there is was section with a few boards that display A3s with standard work documents and employee skill matrices for the area. They call this “MAGIC Garden” because the first letter (in English) of each section of their employee skill matrices are:
- Make-up
- Action
- Growing up
- Instruction
- Captain
“Flower Park” – Customer control area
The employees in this area decided to assign a flower to each region of Japan to associate with customers. Large posters of different flowers and their Japanese name were hung overhead to indicate the inventory that would be shipped to which customer.
Mrs. Ogura shared that to the employees this expresses appreciation for the customer:
“If people just continue to manufacture parts, they will lose sight of the customer”.
Production Board
A huge production board covered a large portion of the wall near the Flower Park area to schedule customer orders and delivery. Staff and managers manually hang large strips of colored material to schedule inventory management and shipping.
Mrs. Ogura emphasized that manual visual systems can be more helpful than automation. She said that 20 years ago the company introduced computers and saw an increase in inventory. They took out the computers and reduced inventory. Now visualization of the work is better and their processes are better.
“Stationery Store” – office area
The office area also uses 5S principles across all areas of the space.
In the supply room, doors were taken off cabinets and kanban cards are in place for replenishment. They call the theme of the supply area a “stationery store” because price tags have been placed on all supplies to make staff aware of the cost of taking certain items. Supply costs have decreases since the staff implemented this.
I found a few photos of the office area in this blog post written in Vietnamese.

Interpersonal skills are essential
Mrs. Ogura explained that one way they have developed the company’s culture has been to focus on interpersonal skills, such as their greeting ritual and giving thanks.
Greeting ritual
The daily “greeting ritual” has been a powerful enabler of team engagement.
She explained that when she took on a leadership role at the company, many front-line employees didn’t have the knowledge, skills, or confidence to greet others (managers, same level staff or even customers).
The leadership team saw this gap and started a daily program to embed skills and habit of how to greet one another.
They see this as the foundation of human relationships, which are essential to their improvement work and management system.
Thank you notes
Mrs. Ogura also shared with us the importance of giving thanks and showing appreciation. For the past seven years, staff and management have been encouraged to write notes of appreciation to each other.
They haven’t thrown away any of the notes and there is a huge mountain of thank you notes in part of the factory. Mrs. Ogrua said that Board members, the President, and VPs look at it every week when they walk through the factory and check in on all of the areas.
While this mountain of thank you notes might not conform to some of the 5S principles, it is important to Mrs. Ogura to keep a visual reminder that people are the most important.
What do you think?
What do you think about how Ogura Metal has implemented 5S principles and TPS?
Have you seen this concept of joy and whimsy in your experiences of Lean practice? Scroll down to leave comments below.
You can more about Ashikaga and 5S in the following posts
- “Upcoming Japan Lean 5S Study Trip: “Best of Ashikaga – Lean Management, Rural Winery, Japan’s First School and More!
- Japan Gemba Visit: Ashikaga Part 1 – the city that uses 5S to revitalize and bring joy to the community
-
Life in Japan: Where clean is beautiful, but 5S is still hard
-
Life in Japan: Visual and audible management to guide everyday life