As a Lean healthcare practitioner and coach, it has been one of my goals while living in Japan to learn more about how Japanese hospitals think about improvement, kaizen, and management.
In one of my very first blog posts, I asked “Are Japanese Hospitals Lean?”. In the past week and a half I’ve been able to explore this topic in more depth with site visits and discussions with leaders at two Tokyo hospitals.
What does “Lean” mean in Japan?
In the 14 months that I’ve lived in Tokyo, I’ve learned that the answer isn’t as simple as answering “Do hospitals (or any Japanese organization) practice Lean or not?” It is more nuanced than that.
I’ve come to realize that it is also important to understand what “Lean” means (or doesn’t mean) in Japan.
First, we must remember that “Lean” is a Western term.
The term “Lean” was coined by American researchers to describe the management and leadership practices they observed at Toyota (and subsequently applied to other companies demonstrating the same philosophies). The term has stuck, although many would say that it is an unfortunate term as it often gives negative connotations of doing more with less, rather than as a leadership approach based on engaging everyone in improvement.
Also, some terms that we use in English to describe “Lean” methodologies or practices in the West, are not what they are known by in Japanese terms. For example, it was pointed out to me that “Value Stream Map” is a term that Japanese would find foreign, but that the concept is one many people in industry would know (although few participants at a Japanese healthcare conference were familiar with the concept or word).
So, if you ask a Japanese person directly if they practice “Lean” they might say no, when in fact they demonstrate many of the elements (see point two below).
Second, “Lean” is not synonymous with “Japanese” management.
What we call “Lean” – starting with the Toyota Production System in the last century – is a blend of some of the best management thinking from both Western and Japanese cultures and practices.
While in Japan, I’ve come to learn that what we in Western societies consider “Lean” is not inherently Japanese. Not all Lean practices are intrinsic to traditional Japanese ways of thinking and not all Japanese businesses are run like Toyota (or other Japanese organizations that we might label as “Lean” practitioners).
As I wrote in a post for the Lean Enterprise Institute’s “Lean Post” last year:
“It’s not easy for the Japanese, just as it isn’t easy in other cultures…. In many ways, some aspects we consider foundational to lean thinking (developing people as problem solvers, leader-as teacher) are counter to traditional Japanese business practices. Toyota and other lean thinking companies are unique in Japan, as are organizations in the West who practice deep lean thinking.
At the same time, there are deep-rooted Japanese qualities that make “Lean” easier to practice and that are demonstrated throughout everyday life such as adherence to rule (or standard work), following kata (or routines), a cultural appreciation of cleanliness, and a deep respect for treating others well.”
Jun Nakamuro has also written about some of these Japanese cultural practices that are fundamental to Lean and the Toyota Productions System, such as hansei (self-reflection) .
Third, Lean application in non-industrial settings in Japan is behind that of other countries.
I anticipate that many of you, myself included when I first moved to Japan, might be surprised to learn that Japanese hospitals and service organizations are seemingly behind the Western world in applying Lean to their operations.
I wrote about this in the same “Lean Post” article cited above, as well as posts on this blog, as it has been one of the stand-out take-aways from my time in Japan after my first six months living here.
Do Japanese hospitals practice “Lean”?
So, back to the second topic of this post: do Japanese hospitals practice what we Westerners would label as “Lean”?
Before moving to Japan in January 2015, I had heard from many people who had visited Japan on study trips that they hadn’t seen evidence of deep “Lean” practice at Japanese hospitals. I have been interested in digging deep to see if this is true from my own experiences, and if so, why?
Commitment to quality and kaizen
Over the past year, I have had a chance to visit and talk with the senior leaders of several Japanese hospitals, all of which who are leaders in Japan in their approach to Quality and application of quality improvement.
Each of these Japanese hospitals demonstrate commitment to quality improvement and kaizen. Their leaders talk about their passion to deliver quality healthcare and their desire to engage more and more people in improvement (kaizen).
Projects, not integrated management system
However, from my gemba visits, conversations with these kaizen-minded healthcare leaders, and attending a kaizen-focused healthcare conference, while quality management practices run deep at many Japanese hospitals, it does not appear that a full Lean management system is yet being practiced in hospitals in Japan.
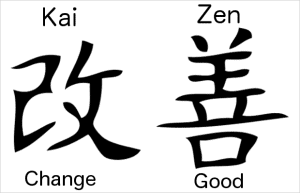
Improvement is talked about in terms of year-long quality improvement initiatives, quality circles and kaizen meetings, rather than an integrated management system that engages frontline staff in everyday improvement and is connected all the way up to the strategy of the organization.
These observations are validated by discussions with a Kaizen Promotion Office Director at one of the hospitals I visited last year and by the Medical Director of Quality at a Tokyo hospital who yesterday offered up some great observations about why this is.
Both of these improvement leaders have indicated that they want to bring more of the management philosophy of Japanese industry (such as Toyota) into their hospitals’ practices.
My friend Mark Graban has written many posts about his experiences visiting hospitals in Japan, and his observations align with my own. Mark and I also talked about our mutual observations about Lean generally in Japan in a podcast that I recorded with him back in October.
Lessons on kaizen, quality, and Lean management in hospitals
In upcoming posts over the next few weeks, I’ll share with you what I’ve learned through discussions with two Tokyo hospitals in the past ten days. I visited a smaller Tokyo hospital to talk with the CEO and Medical Director of their Medical Quality Improvement Office last week [update: this post is now available], followed by a follow-up conversation yesterday with the Medical Director and the Manager of the Quality Improvement Department of a large international hospital in Tokyo [update: this post is now available].
Both were interesting and insightful experiences.
You can also read about my earlier experiences learning about hospitals and healthcare in Japan.
What do you think?
Are you surprised to learn about Lean practices in Japan? What questions do you have as I continue to connect with healthcare leaders in Japan?
Please share your comments in the section below.