Quality improvement approaches in Japanese hospitals
It probably surprises many Westerners, where books such as Lean Hospitals by Mark Graban and organizations such as Thedacare and Virginia Mason are well known, to learn that the practice of the Toyota Production System (TPS) or “Lean” management is not common in Japanese hospitals.
While quality improvement is not a new topic to Japanese healthcare leaders, one of the most intriguing topics for me to learn about while living in Japan was why business management methods – particularly “Lean management” as developed initially by Toyota and practiced by extensively by Japanese manufacturing organizations – are not prevalent in Japanese hospitals or service industries.
One of my most popular blog posts published six months ago, “What does “Lean” mean in Japan? Are Japanese hospitals practicing “Lean”?”, summarizes many of my observations about Lean in Japan.
Toyota methods becoming more popular in hospitals
Many Japanese hospitals have several decades of practice with Total Quality Management (TQM) approaches. However, this focus on quality is still project based and less about a systemic management system.
But hospitals are starting to get interested in “Lean” approaches, particularly from learning from their U.S. counterparts.
I also recently found out about new program in Japan where Toyota leaders are starting to directly train Japanese doctors in Toyota Production System methods. After publishing a blog post about this new Toyota program in healthcare, I realized that I hadn’t published another post that I had drafted six months ago while I was still living in Tokyo.
The following post is based on a conversation with a physician leader at a Tokyo hospital who is leading quality improvement activities and was interested in learning from me about how Toyota principles can be applied in healthcare.
Transpacific Lean healthcare exchange
Since the beginning of this year, I have developed a collegial relationship with St. Luke’s Medical Director of Quality and one of the Quality Improvement (QI) Managers.
We’ve met to exchange ideas about quality and process improvement and to learn about each other’s approach to improving healthcare. Both of these QI leaders speak excellent English, which facilitates our collegial thought exchanges.
At one of our meetings earlier this year I asked the Medical Director directly why Toyota-type methods were not common in Japanese hospitals. This is what he explained.
Two schools of improvement in hospitals
St. Luke’s Medical Director said that two QI trends have emerged in Japanese healthcare by two different groups of quality improvement leaders.
1. Clinical epidemiology leaders
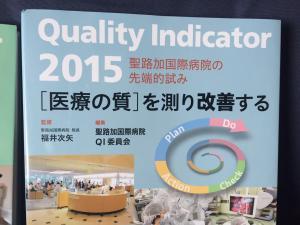
The first group of quality improvement leaders in healthcare consists of clinical epidemiologists.
They are focused on:
- bringing evidence-based medicine (EBM) to Japan
- monitoring quality indicators
- determining the gap between clinical guidelines and current state
- using Total Quality Management approaches (such as Quality Circles and year-long projects) to close the gap
This group of clinical epidemiology-focused leaders has grown in Japan and explains the quality improvement approach of many of the hospitals that I’ve visited in Japan have been using.
Three leading epidemiology-focused hospitals
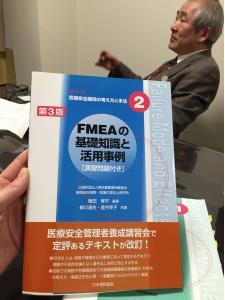
St. Luke’s Hospital‘s President is one of these clinical epidemiologists and has done tremendous work over the past two decades in advancing the awareness of clinical quality and evidence- based medicine in Japan. I have written in detail about St. Luke’s approach to clinical excellence and quality improvement. The Medical Director of Quality and the QI manager are looking to build on the TQM approach and bring in more improvement concepts from the manufacturing industry.
Nerima General Hospital in Tokyo also has has a decade-long “Medical Quality Improvement Program”, which has been led by it’s physician CEO and medical directors. They have published a series of quality improvement books to teach their staff and others about QI tools.
Aso Iizuka Hospital on the island of Kyushu has a decades-long Quality Circle Practice. However, in the past few years has put greater focus on Lean and Toyota-style approaches through collaboration with Virginia Mason Medical Center. Aso Iizuka put on a great healthcare conference last year that brought together quality improvement leaders form both approaches.
2. Management-trained leaders
The Medical Director explained that the second group of quality improvement leaders in hospitals consists of individuals who are originally trained in management and/or came from industrial backgrounds. Currently, this group is much smaller in Japan than the clinical epidemiologists.
One reason that this group is less common, as I’d learned last year, is that senior leaders in Japanese hospitals tend to be doctors, and the most senior leader (usually the hospital president) must by law be a physician. Most of these physician leaders come from academic backgrounds, and few few have had prior business or management training.
When I’ve asked people over the past year about why approaches used by Toyota and other successful Japanese industrial organizations aren’t pervasive in hospitals, one of the common answers is that the senior leaders have not been exposed to these types of management practices.
Instead Japanese healthcare leaders tend to gravitate towards a focus on the clinical side of quality, in which they have been trained.
I suppose that this isn’t completely unlike how quality improvement has been traditionally approached in the U.S. and other Western countries, except that in the past decade (or for some, a decade and a half) an increasing number of hospital have been embracing Lean.
It has just been surprising to me that for a country that is so ahead of Lean management in manufacturing, that they have been slow to adopt this type of thinking in healthcare.
Toyota’s Hospital in Toyota City, Japan
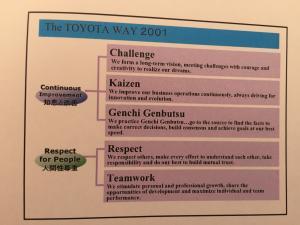
These observations offered by St. Luke’s Medical Director about QI approaches are consistent with what a senior leader at Toyota Memorial Hospital’s shared with me a month later when I went to visit in April.
The Toyota Memorial executive is one of those rare “management trained” leaders who comes directly from Toyota Motor Corporation’s Human Resources division. Toyota Memorial is leveraging this leader’s (a a few others’) deep expertise in the Toyota Way and is one of the reasons I consider Toyota Memorial to be “the most Lean hospital in Japan”.
It is rare in Japan to have a senior leader be someone from outside of healthcare (although the President of Toyota Memorial Hospital is an academic physician).
I’ve written a five-part series about my day-long visit to Toyota Memorial and how they are using their Toyota management-trained leaders to accelerate quality and patient care delivery improvements.
Improving quality improvement approaches
During this same conversation, the Medical Director and QI Manager asked me to share some more “industrial” approaches to TPS-style management practices. They want to improve their approach to improvement and augment their clinical epidemiological QI focus with one that addresses all aspects of the delivery system and engages people in daily problem solving.
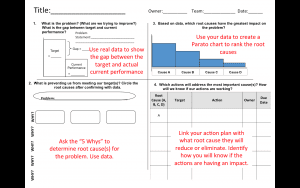
Lean to engage the frontline in improvement
In particular, they wanted to more deeply engage frontline staff in PDCA and problem solving. They shared in an prior meeting that they had introduced management visibility boards a few months earlier. But right now only management was really engaging with the boards and often they were not updated.
I shared with them some of my experiences helping many different hospitals and health systems start practicing Lean, including a problem solving tool that can help foster problem solving at the unit level.
You can get a blank template of the same simple four-box problem solving tool that I shared with this Japanese hospital by clicking here!.
In a future post, I’ll write more about I’ve discussed with and learned from these Japanese QI leaders about Japanese healthcare, leadership and continuous improvement.
The power of bringing clinical and management together
I keep reflecting that the Japanese are poised to really transform how healthcare is delivered in their country – and to contribute to the global dialogue of how to deliver quality care – if they can integrate both approaches to quality improvement!
I look forward to continuing to see how Japanese hospitals can combine their clinical QI expertise with “manufacturing” leadership as they seek to “improve improvement”.
What do you think?
As always, I welcome your comments of what you are thinking about or what questions you have as I explore topics of leadership, Lean and life in Japan (and beyond).