A vision realized….and continues!
Just three weeks ago, I was in the midst of leading a week of learning, culture, and fun with a fabulous group of 17 lean practitioners in Japan on the 2nd KBJA Japan Study Trip!
When I moved to Japan 4.5 years ago, it was with the intention to learn and share as much as possible as a Lean thinker living in Japan, which was the genesis of this blog. Since returning to the U.S. nearly 3 years ago, it gives me great joy to offer study trips to Japan to share my experiences, connections, and insights directly with you (and of course, through this blog as well).
There are so many highlights and stories that I want to share with you from the recent KBJA Japan Study Trip from May 2019. My intention is to write more in depth about some of our experiences and share them here with you.
Today I want to share some of the highlights of the week with you.
You can also find stories and photos on LinkedIn and Twitter under the hashtags #KBJAJapan and #JapanLeanStudyTrip.
Come to Japan with me!
It gives me great pleasure to be organizing and leading another KBJA Japan Study Trip in May 2020.
Join me for an experience of a lifetime!
Mr. Yoshino is confirmed to join the trip for most (if not all!) of the program, and many of the experiences highlighted below will be part of 2020 itinerary.
Click here to learn more about the next KBJA Japan Study Trip May 10-16, 2020.
Special super early bird price discount is available for a limited time. Block your calendar for May 10-16, 2020 and apply today!
KBJA Japan Study Trip 2019
Our group of 17 participants came from around the world including the United States, Chile, the Netherlands, and Australia. Our mix of 10 women and 7 men, coming from a wide mix of industries and backgrounds (pharmaceutical, healthcare, manufacturing, water management, consulting, and more), led to a richness of discussion and shared experience.
Most people didn’t know each other before the start of the trip and we developed a wonderful community, learned deeply, and had a lot of FUN!
Again, we were so fortunate to have Isao Yoshino, my friend and 40+ year Toyota leader, join us for multiple days of the trip – not just for presentations, but for site visits, meals, bus journeys, and conversation.
And thank you to my co-partner in planning, leading, and serving as the interpreter for this trip – Mami Takeda!
To learn some of the planning that led to the 2019 KBJA Japan Study Trip program, you can also check out these prior posts:
- Top 10 Experiences from the Japan Lean Study Trip – May 2018
- Japan Lean Study Trip – Focus on People!
- Highlights from Japan: Happiness is our Purpose
Measure of success: smiles and action
My measure of success for the 2019 Japan Study Trip echos what Mr. Yoshino says was his measure of success when leading the NUMMI management training program in Japan in the 1980s (I will write more about this in a future blog, and will be sharing in our book coming out later in 2019):
- Smiles of joy (or tears of joy) at the end (at least 80%)
- At least 1-2 actions each person would take back and apply at the end of the experience.
Results – Smiles all around and take-aways abound
You can see by all the smiles throughout that we exceeded the mark on the first measure.
I asked each participant to make a clear goal for what they will do following the trip – and to make it visual on a daruma doll that I gave to everyone on Friday.
Highlights from the KBJA Japan Study Trip Program 2019
We had a full week of nearly nonstop learning experiences, discussion, meals, and culture. I was excited to introduce some new cultural elements to this year’s program such as staying at a traditional Japanese ryokan and visiting my favorite temple in Japan – the daruma temple!
Key themes across the week were more people-centered topics such as leadership, people development, customer service, happiness/joy, and respect. Of course we saw many tools and production principles in action – but ultimately, this trip was about people!
This visual summary from trip participant Shawn Carner of Genentech is a great summary of the week.
Sunday
We convened on Sunday with a welcome dinner in Nagoya. It was a fun way to get to know each other and work off jet lag over a wonderful meal.
Monday
The first theme of our trip was on Japanese culture and leadership.
Orientation and foundational learning
We kicked off the formal program on Monday with orientation, including introductions (including “two truths and a lie”), learning important greetings and customs, and walking through learning journey for the week.
Mr. Yoshino provided a foundational overview about Toyota culture and leadership to set the context.
I also introduced a framework for participants to consider what they were learning and observing and how much influence Japanese culture and Toyota-specific culture have on Lean thinking and practice.
Isao Yoshino – 40+ year Toyota leader – joined our group today from 8am until after dinner for lecture, discussion on bus and at meals, and commentary on gemba visits! He joins for 3 other days this week! #KBJAJapan https://t.co/onzrrV0qNw pic.twitter.com/iKPsS4soOi
— Katie Anderson (@kbjanderson) May 13, 2019
Kura Sushi
Then we were off for an early lunch at Kura Sushi. Check out my post about this “lean” Japanese fast food experience!
Kura Sushi doesn’t disappoint! Lean concepts and “lean” healthy fast food! #KBJAJapan https://t.co/onzrrV0qNw pic.twitter.com/ItTyH4QsAh
— Katie Anderson (@kbjanderson) May 13, 2019
Elementary School visit
We visited a local elementary school to learn about how the concepts of “mottainai” (deep regret for waste) and respect for community and environment are instilled in children at an early age. It is always wonderful to interact with the children and get to see a slice of “real life”.
This cultural value of “no waste” is embedded in Japanese children at an early age, as demonstrated by how schoolchildren are taught to serve and eat lunch together. Also, the values of cleanliness and taking care of community, which I have written about previously, is taught through all students and staff taking part in daily cleaning of the school.
Learning the Japanese concepts of regret for waste and respect for environment by visiting a Nagoya-area elementary school to observe lunch and cleaning rituals. #KBJAJapan https://t.co/onzrrV0qNw pic.twitter.com/ChDV3uChWp
— Katie Anderson (@kbjanderson) May 13, 2019
Theme: follow the Toyota supply chain
After waving enthusiastically goodbye to the school, we then journeyed to Toyota City where we began our “Toyota supply chain” learning journey of the deep connections between Toyota and its suppliers, and observe how the Toyota Way has been taught and developed from Toyota down to its suppliers.
Isuzu Steel – Toyota Tier-3 Supplier
We visited Isuzu Steel on Monday afternoon, which cuts large coils of steel to be prepared for stamping. Isuzu has some wonderful examples of kaizen, safety procedures, people development, kanban, visual management, and innovation for the future.
Toyota Tier 3 supplier – focus on safety, long-term view, visual boards, SMED, people development, and leadership! #KBJAJapan https://t.co/onzrrV0qNw pic.twitter.com/e9wiwnyuNW
— Katie Anderson (@kbjanderson) May 13, 2019
After returning to our hotel and some formal reflections on the day, most of us headed out to dinner together (and I got to really test out how much Japanese I remembered!).
Fun evening outing for a dinner of tonkatsu at the end of a full day! Day 1 of #KBJAJapan Study Trip wrapped up! https://t.co/onzrrV0qNw pic.twitter.com/X5FQLwe1yz
— Katie Anderson (@kbjanderson) May 13, 2019
Tuesday
Some of us started the day with a walk to a local shrine in Nagoya, where Mami-san taught the group the etiquette of visiting shrines and temples.
After breakfast, we continued the Toyota supply chain experience that we began on Monday.
Mifune – Toyota Tier-2 Supplier
Our morning visit was to Mifune, a Tier-2 supplier that stamps smaller parts from steel supplied by Isuzu and others.
It was great to see the changes since I was there last year and how they have set up a new factory area. The new SMED die changeover was a dance to watch!
So many highlights to share here in a future post – visual management, hoshin, people engagement/development, SMED, kanban, new factory layout, and more.
Amazing to see the changes at Mifune (Toyota Tier 2 supplier) and always inspirational to spend time with Mr. Umemura. His leadership, passion, and joy is contagious. #KBJAJapan https://t.co/onzrrV0qNw pic.twitter.com/MM7C7Fp6IZ
— Katie Anderson (@kbjanderson) May 14, 2019
The energy and passion that Mr. Umemura, the founder and chairman of Mifune, has for his company and people is inspirational. He personally toured our group around the factory and enthusiastically talked with us about each visual board, production principle, and process that we observed.
Mr. Umemura joined us, along with Mr. Yoshino, at lunch for further conversations – and another delicious meal.
Toyota Motor Corporation – Toyota City
After lunch we went to Toyota were we visited the Tsutsumi Plant and Kaikan museum. There really is nothing like watching Toyota in action and to see so many of the principles applied!
Toyota Kaikan Museum following our visit to Toyota’s Tsutsumi plant. Always inspirational and aspirational! #KBJAJapan https://t.co/onzrrV0qNw pic.twitter.com/fUywJehkPS
— Katie Anderson (@kbjanderson) May 14, 2019
We wrapped up Tuesday with further reflection and discussion, and dinner out for shabushabu.
Wednesday
Theme: long-term view, happiness, and customer service
Ina Food Industries
As I shared in February, I was beyond thrilled that Ina Food Industries offered to host our group. Located up in the mountain in the Nagano Prefecture, Ina Food is a company admired by many Japanese leaders for its focus on happiness and long-term perspective (see my recent blog post to learn more).
We were privileged that former Chairman and author of “Tree Ring Management: Take the Long View”, Mr. Hiroshi Tsukakoshi, was available to speak with us.
It was a deep honor to meet Tsukakoshi-sensei, a man whom Toyota leaders consider their teacher, as well as his son Ryo Tsukakoshi and the staff and managers.
At the end of the presentations and discussions, Hiroshi Tsukakoshi signed books for us!
Our visit was the epitome of Japanese hospitality and customer service (omotenashi). Tsukakoshi-sensi joyously toured us through the garden grounds, the art galleries, and restaurant that he developed for his community to enjoy.
After enjoying lunch on-site, Ryo Tsukakoshi led our tour through the manufacturing facility and shared examples of kaizen (continuous improvement) and kaiteki (comfortableness).
Mr. Yoshino commented “I think Ina is far more advanced than Toyota!”
TESSEI Shinkansen “7-Minute Miracle” Changeover
We drove from the mountains to the heart of Tokyo, where we continued our theme of omotenashi by learning from Mr. Yabe, the former President of the Japan Railway East cleaning company TESSEI.
We heard how TESSI transformed its business practices to create the “7-minute miracle” changeover of the Shinkansen trains though a revitalization of employees’ spirit.
What a way to end Day 3 of the #KBJAJapan Study Trip! Customer service, servant leadership, and taking kaizen to the next level with Mr. Yabe. Plus the 7-minute miracle Shinkansen changeover. #japanleanstudytrip pic.twitter.com/U1LWs58Tgp
— Katie Anderson (@kbjanderson) May 15, 2019
The passion Mr. Yabe, former president of TESSEI, has for the TESSEI employees and delighting customers through “omtenashi” (Japanese hospitality) is palpable.
After a formal lecture and discussion with Mr. Yabe, we went up to the train platform to watch the changeover happen several times, with narration by Mr. Yabe.
Thursday
Themes: Female leadership, healthcare, innovation and joy
Thursday morning we boarded the Shinkansen and began our journey to the town of Ashikaga – the “5S City” I’ve come to know well over the past four years.
And we are off on the Shinkansen to visit a hospital & Ogura Metal in Ashikaga (the “5S city”) and enjoy a traditional mountain area ryokan & onsen tonight! #KBJAJapan pic.twitter.com/t7MmIm18Nl
— Katie Anderson (@kbjanderson) May 15, 2019
We were joined by my friend Toshiko Kawanami, who was my first introduction to Ashikgaga in 2016 when I was living in Tokyo.
Now in her 70s, “Nami-san” shared her experiences as a successful female business leader and the challenges she faced in a predominantly male-dominated society.
Ashikaga Red Cross
Dr. Satoru Komatsumoto, the Director of the Ashikaga Red Cross Hospital, spoke to our group in English about healthcare in Japan, his hospital’s focus on quality, and his leadership philosophy, and then personally toured us throughout the hospital.
A highlight was talking with the nurses in one of the nursing units about their experience with their “mixed model” wards (35 patient beds per unit with mixed diagnoses, whereas in many hospitals wards are separated by patient type such as “surgical”, “cardiac”, “acute”, etc.).
Ogura Metal
Over lunch, we were joined by Mrs. Noriko Ogura – who showed us photos of her early career as a ski racing announcer for television!
Mrs. Ogura hosted us at Ogura Metal and shared Ogura Metal’s journey, as well as her personal experiences being a female business leader in Japan (note: recently she was invited to speak with Prime Minister Abe about how to increase female leadership in Japanese businesses).
I value her friendship and appreciate getting to spend time with her and Nami-san whenever I am back in Japan.
You can see some highlights from my prior visits to Ogura Metal here. They are a wonderful example of humble leadership, people engagement, visual management, and creativity and joy!
It had been a year since I had last visited Ogura Metal and it was great to see the changes they had made, including new products and production line!
Theme: Culture, reflection, and goals
With our site-visits concluded, we focused the remainder of the trip on Japanese culture, reflection, and goal setting.
Thursday night we stayed at a Japanese ryokan for the full omotenashi experience!
We wore our yukata (robes) to our celebration dinner, and people enjoyed the onsen and post-dinner karaoke at the ryokan!
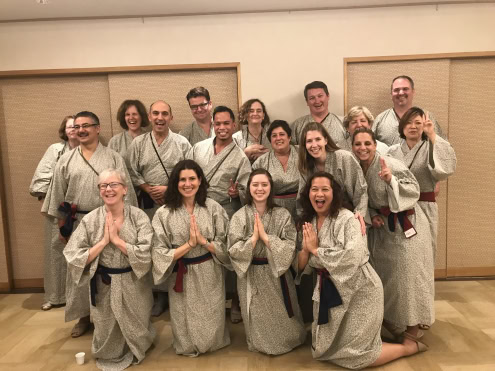
Friday
Cultural excursions to shrines and temples
After a more leisurely morning, where many of us walked to the local shrine or enjoyed a morning onsen, we departed the ryokan to the town of Takasaki.
A delight of mine was to share my favorite temple in Japan – Shōrinzan Daruma-ji, the daruma temple – with our group as well. As many of you know, I’m obsessed with daruma dolls and was so happy to bring everyone to the temple!
Mr. Yoshino and Final Discussion
After another Shinkansen journey (always fun!), we had our final lunch together before embarking on our final trip wrap-up.
Mr. Yoshino joined us from Nagoya to talk about hoshin kanri (goal deployment), followed by a deep reflection and discussion on take-aways from the week.
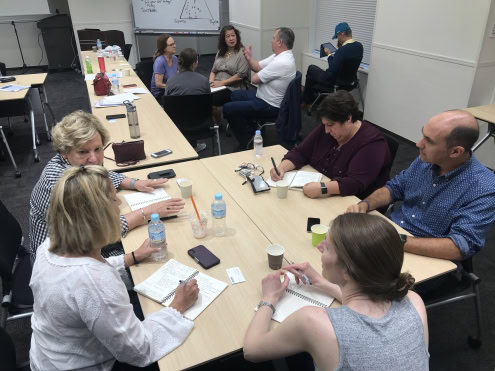
At the end, I gave all participants a daruma (see main photo in this post) to set their goals and intention for practice following this amazing week together.
And of course, we had one more final celebration together at a favorite fish izakaya under the train tracks in Tokyo!
That’s a wrap of the #KBJAJapan Study Trip. Amazing end to an amazing week of learning, culture, and fun! Night in a ryokan, daruma temple, & discussion & dinner in Tokyo. Join me next year! https://t.co/8YxLhhckDr pic.twitter.com/kPTFXe0Xpl
— Katie Anderson (@kbjanderson) May 18, 2019
Thank you Tracy O’Rourke and Elisabeth Swan for the signed copies of your book for everyone on the trip!
Thank you @RourkeTracy & @consultswan for the signed copies of your book for all participants on the #KBJAJapan Study Trip! What a wonders gift! @GoLeanSixSigma https://t.co/onzrrV0qNw pic.twitter.com/ZKd60ZEpzz
— Katie Anderson (@kbjanderson) May 14, 2019
Amazing week – I have a smile on my face!
What a week! I’ve had a smile on my face while reliving all of these memories while writing this post.
I personally want to do a deeper dive into some of the details to share with you. Each of these experiences is worthy of its own post.
I am so happy to have shared this week with a wonderful group of people, and to be able to offer these special experiences with others.
Join me in May 2020
Please join me next May 2020 for another KBJA Japan Study Trip! I cannot wait to share another amazing week with *you*.
Visit the Japan Trip page on this website to learn more – or email directly ([email protected]).
I’m already starting to put together the program and know that it will be another amazing experience. Super discounted price special available for a limited time too, so apply today!